Carrosserie Auto Mercedes CLS 218
Pour la gamme 218, tous les composants de la carrosserie Auto sont de conception nouvelle.
On retrouve parmi les points essentiels adoptés lors de la phase de développement de la carrosserie Auto nue de la nouvelle classe CLS :
- Un accroissement supplémentaire de la rigidité et de la résistance de la cellule passagers
- Des zones de déformation améliorées de façon ciblée dans la structure du bloc avant et du bloc arrière
- Grande facilité de réparation du fait de parties avant et arrière démontables, s’accompagnant d’une réduction du poids par la mise en œuvre d’un profilé extrudé en aluminium (avant) ou d’acier à haute résistance (arrière)
- Bonnes conditions de montage pour les organes moteur et l’essieu avant grâce au berceau intégral vissé
- L’utilisation du procédé de soudage MIG permet de renoncer complètement aux cordons de soudure MAG. Ceci a permis d’améliorer très nettement la qualité de fabrication et la résistance à la corrosion
- La proportion en poids des tôles d’acier à haute résistance dans la carrosserie nue est passée de 45 % à 72 %, avec une utilisation renforcée de nouveaux types d’acier
Quels sont les matériaux utilisés pour réaliser les carrosserie Auto ?
La tôle d’acier a été retenue comme matériau pour la plus grande partie de la carrosserie Auto nue. Les ailes avant, le capot moteur et le couvercle de coffre sont en aluminium. La part de l’aluminium, exprimée en poids de la carrosserie Auto nue, est donc de 8 %.
Le berceau intégral en acier à haute résistance a été vissé avec les longerons avant en vue de la fixation de l’essieu avant, de la direction et du moteur.
Le logement de roue de secours est réalisé en thermoplastique renforcé de fibres de verre (GMT).
Quels sont les principaux éléments de la carrosserie ?
Bloc avant
La structure avant de la gamme 218 est dotée d’un module avant monté sur le véhicule, qui se compose de :
- Un profilé extrudé en aluminium
- Un caisson anticollision monopièce en aluminium, reliant les deux longerons avant
- Une ossature multi pièce matière plastique renforcée de fibres de verre et en tôle d’aluminium pour la fixation des projecteurs, du pare-chocs, du réservoir d’eau de lave-glace et des serrures de capot moteur
Le module avant complet est assemblé par vissage sur la structure avant, tout comme les différents composants du module avant entre eux. En cas d’endommagements, cette construction permet de remplacer les pièces à peu de frais, sans travaux de soudage.
La fixation du bloc avant à la cellule passagers est assurée maintenant au moyen de quatre, et non plus trois (prédécesseur) éléments de tôle assemblés.
Cellule passagers
Toute la conception de sécurité de la carrosserie s’articule autour de la cellule passagers extrêmement résistante, qui joue le rôle d’une cage de sécurité. Les points suivants contribuent principalement à sa haute résistance face aux sollicitations d’un accident (collisions frontales, latérales et arrière ainsi que retournements) :
- La mise en œuvre accrue de tôles d’acier à haute résistance, modernes à haute résistance, à ultra-haute résistance, à ultra-haute résistance et formées à chaud, ainsi que de tôles d’épaisseurs échelonnées
- L’utilisation de matériaux et d’épaisseurs de tôles résistant aux sollicitations pour les composants ou les zones de structure fortement sollicités en cas d’accident
- Une forme et une conception de la section optimisées
Portes
Les portes nues et l’encadrement des vitres latérales sont dotés d’une doublure intérieure en tôle d’aluminium avec renforts extérieurs (profilés extrudés et pièces thermoformées). La surface en tôle portant la charnière est séparée de la doublure, comme sur la Mercedes Classe E actuelle. On peut ainsi utiliser, avec seulement un faible poids supplémentaire, une tôle plus épaisse en vue d’améliorer le guidage des forces dans la zone de la charnière.
Pour accroître la rigidité et la résistance des portes, des profilés de renfort sont soudés dans la zone de l’encadrement et de la bordure. Les portes comportent en outre deux profilés extrudés pointés et collés, disposés dans le sens diagonal et longitudinal, afin de
réduire la profondeur de déformation en cas de collisions latérales et d’améliorer la résistance au flambage.
Bloc arrière
L’essieu arrière multibras, le réservoir de carburant et le logement de roue de secours sont disposés sur la nouvelle Classe CLS de façon similaire au modèle précédent. Malgré cela, des différences apparaissent dans la géométrie des structures de carrosserie Auto
arrière. Cela est très net au niveau de l’aménagement des structures dans la zone de l’ouverture de la trappe de chargement au niveau de la paroi arrière de l’habitacle, des longerons arrière, du logement de la roue de secours et de la partie arrière.
Les éléments de fixation du dossier ou des charnières et serrures du dossier rabattable (option) de la banquette arrière sont supportés par une structure porteuse périphérique, qui est soudée à gauche et à droite avec la doublure de la paroi latérale, en bas
avec la tôle de plancher et qui est reliée en haut avec la plage arrière par un procédé d’assemblage par emboîtement. La structure porteuse mentionnée contribue à améliorer encore la résistance à la torsion de la carrosserie Auto nue.
Afin d’augmenter la résistance, d’optimiser le travail de déformation et d’améliorer la tenue à la déformation, les longerons arrière en plusieurs parties réalisés en acier à très grande résistance sont dotés, comme sur le modèle précédent, d’une section fermée
continue aux épaisseurs de tôle échelonnées.
La partie arrière est constituée d’un support résilient en acier avec zone de déformation intégrée. Afin d’optimiser le poids, de l’acier laminé flexible à ultra-haute résistance est utilisé de manière à pouvoir réaliser les zones extrêmement sollicitées dans une plus grande épaisseur que les zones faiblement sollicitées.
Pour le logement de roue de secours, on utilise comme sur le modèle précédent pour des raisons de poids et de protection anticorrosion une matière plastique (thermoplastique renforcé de fibres de verre).
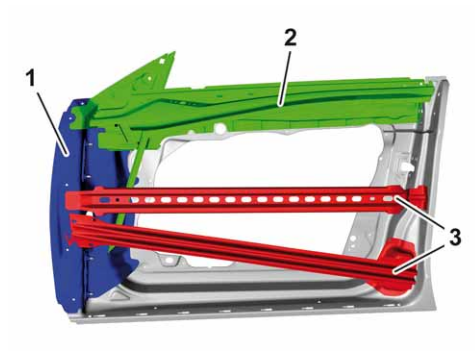
1 Surface de tôle portant la charnière
2 Renforts cadre de vitre et bordure
3 Profilés de renfort disposés dans le sens diagonal et longitudinal
Plancher
Le plancher de la cellule passagers comporte une partie en tôle, trois parties étant reliées entre elles par soudure laser, déjà avant le formage. La partie centrale, dont l’épaisseur de tôle est la plus forte, constitue le tunnel et par conséquent la colonne vertébrale de l’ensemble du plancher. Des renforts massifs supplémentaires sont fixés sur le tunnel. Le plancher est maintenant doté de longerons de part en part en
vue d’améliorer le guidage des forces dans la structure de plancher. Le plancher, à gauche et à droite du tunnel, est raidi par l’intérieur, avec :
- Des profilés de renfort entre la doublure des longerons avant et le tunnel ou entre le tunnel et les longerons latéraux
- Une traverse résistante servant au positionnement des sièges et à l’appui transversal sur le tunnel dans le cas d’une collision latérale
- Une autre traverse au niveau des montants B
La jonction au plancher arrière est constituée comme sur le modèle précédent de la traverse de banquette arrière conçue ici de part en part et munie de renforts
supplémentaires, offrant une résistance spécifique aux collisions latérales.
Protection anticorrosion
La protection anticorrosion longue durée est assurée par une galvanisation complète des éléments de carrosserie Auto en acier. Les zones de la structure particulièrement exposées à la corrosion font l’objet d’une protection supplémentaire des corps creux.
En complément de cela, on a déjà effectué lors de la fabrication des tôles d’acier, outre la galvanisation normale, les mesures de protection suivantes :
- Utilisation de tôles d’acier à enduction organique
- Peinture par trempé cataphorétique
- Étanchéification des soudures
Protection du dessous de caisse
En raison du revêtement complet du dessous de caisse en Pentalaminat, on a renoncé à une protection de dessous de caisse en PVC. Les avantages sont les suivants :
- Résistance de l’air plus faible
- Interchangeabilité en cas d’endommagement (facilité de réparation)
- Démontabilité pour le recyclage du véhicule
- Meilleure résistance aux coups (protection anti-gravillons)
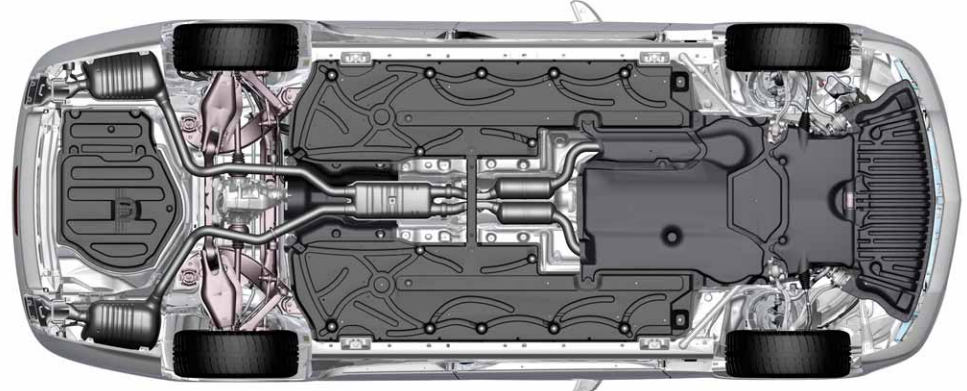
Parcours de la force en cas de choc frontal
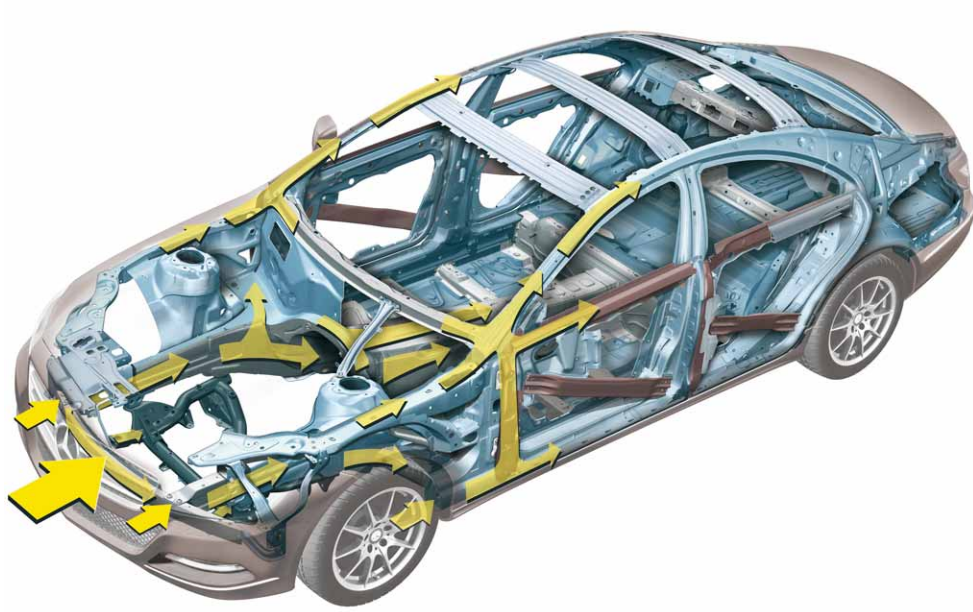
Parcours de la force en cas de choc latéral
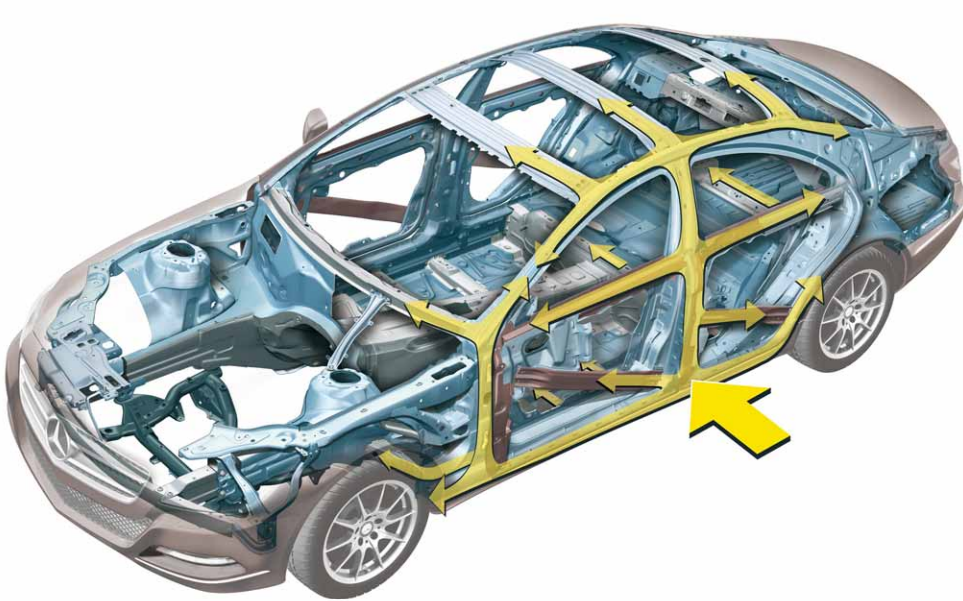
Plaque constructeur et numéro d’identification du véhicule (FIN)
La plaque constructeur est apposée sur le côté droit, latéralement dans l’encadrement de porte.
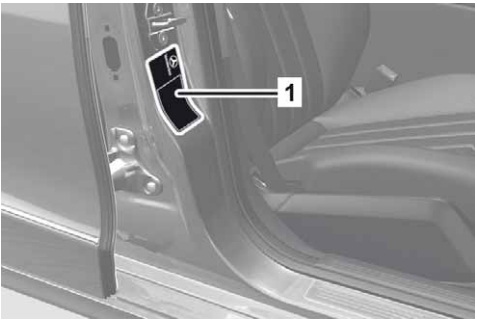
En plus de la mention sur la plaque constructeur, le numéro d’identification du véhicule (FIN) est frappé dans la carrosserie. Il est apposé en bas devant le siège passager sur la traverse de siège. Pour vérifier le FIN, il faut repousser le siège passager complètement vers l’arrière et basculer le cache (9) dans le revêtement de plancher vers le haut. Le
numéro d’identification du véhicule (10) est maintenant visible.
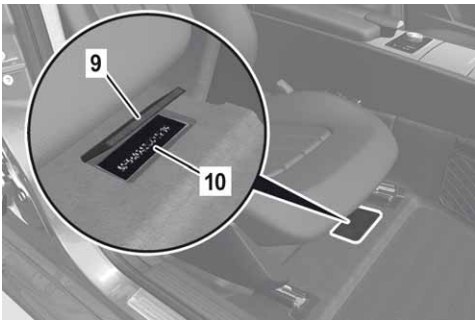
Leave a Reply